Simulation Results for “Integration of Plant and Microbial Oil Processing at Oilcane Biorefineries for More Sustainable Biofuel Production” Publication
Themes: Conversion, Sustainability
Keywords: Life Cycle Assessment, Modeling, Software, Technoeconomic Analysis
Citation
Cortés-Peña, Y.R., Woodruff, W., Banerjee, S., Li, Y., Singh, V., Rao, C.V., Guest, J.S. June 9, 2024. “Simulation results for ‘Integration of Plant and Microbial Oil Processing at Oilcane Biorefineries for More Sustainable Biofuel Production’ publication” Zenodo. DOI: 10.5281/zenodo.11536864.
Overview
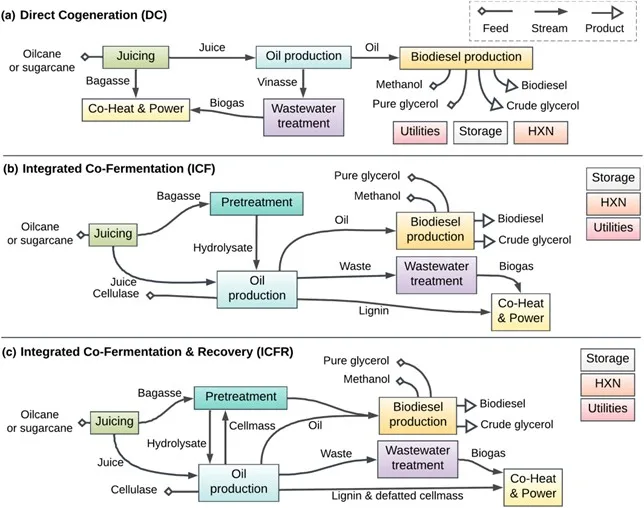
Oilcane—an oil-accumulating crop engineered from sugarcane—and microbial oil have the potential to improve renewable oil production and help meet the expected demand for bioderived oleochemicals and fuels. To assess the potential synergies of processing both plant and microbial oils, the economic and environmental implications of integrating microbial oil production at oilcane and sugarcane biorefineries were characterized. Due to decreased crop yields that lead to higher simulated feedstock prices and lower biorefinery capacities, current oilcane prototypes result in higher costs and carbon intensities than microbial oil from sugarcane. To inform oilcane feedstock development, we calculated the required biomass yields (as a function of oil content) for oilcane to achieve financial parity with sugarcane. At 10 dw% oil, oilcane can sustain up to 30% less yield than sugarcane and still be more profitable in all simulated scenarios. Assuming continued improvements in microbial oil production from cane juice, achieving this target results in a minimum biodiesel selling price of 1.34 [0.90, 1.85] USD∙L−1 (presented as median [5th, 95th] percentiles), a carbon intensity of 0.51 [0.47, 0.55] kg CO2e L−1, and a total biodiesel yield of 2140 [1870, 2410] L ha−1 year−1. Compared to biofuel production from soybean, this outcome is equivalent to 3.0–3.9 as much biofuel per hectare of land and a 57%–63% reduction in carbon intensity. While only 20% of simulated scenarios fell within the market price range of biodiesel (0.45–1.11 USD∙L−1), if the oilcane biomass yield would improve to 25.6 DMT∙ha−1∙y−1 (an equivalent yield to sugarcane) 87% of evaluated scenarios would have a minimum biodiesel selling price within or below the market price range.
Data
Zenodo – Includes baseline and target fermentation performances and detailed reports
GitHub – BioSTEAM biorefinery for canes.